What is a Ball Grid Array?
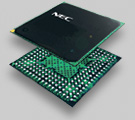
BGA (Ball Grid Array) inspection using JTAG
Disadvantage of BGAs is that, once the package is soldered down, it is very difficult to look for soldering faults. X-ray machines and special microscopes have been developed to overcome this problem, but are expensive. If a BGA is found to be badly soldered, it can be removed in a rework station, which is a jig fitted with infrared lamp (or hot air), a thermocouple and a vacuum device for lifting the package. The BGA can be replaced with a new one, or can be refurbished or reballed. Packets of tiny ready-made solder balls are sold for this purpose.
BGA inspection is one area of the manufacturing process that has raised a considerable amount of interest since the introduction of the first BGA components. BGA inspection cannot be achieved in the normal way using straightforward optical techniques because, quite obviously, the solder joints are underneath the BGA components and they are not visible. This creates problems for BGA inspection. It also created a considerable degree of unease about the technology when it was first introduced and many manufacturers undertook tests to ensure that they were able to solder the BGA components satisfactorily. The main problem with soldering BGA components is that sufficient heat must be applied to ensure that all the balls in the grid melt sufficiently for every BGA solder joint to be satisfactorily made.
Due to cost of X-ray BGA inspection, electrical testing is very often used. Very common is boundary scan testing using IEEE 1149.1 JTAG port.